feuerlibelle
Aktiv
Nein nicht schon wieder Kipphebelböcke mag der Eine denken. Ich gebe zu, ich mochte auch kaum noch etwas dazu sagen!
Seit Monaten bin ich an den Dingern dran. Was sich hier so einfach präsentiert, war ein ganz steiniger Weg! So viel Pleiten, Pech und Pannen, das glaubt man nicht.
Zielsetzung war ein einteiliger Kipphebelbock der das Klappern im Ventiltrieb minimiert.
Wie geht man an so etwas heran? Für Maschinenbauer eine klare Sache, für den Laien möchte ich es erläutern.
Als erstes muss man sich klar machen, welche Kräfte wo herrschen und wie deren Verlauf ist. Da haben wir zu einen die Vorspannung der Stehbolzen zum Motor, zum anderen die Wärmedehnung in der 90 Grad Achse zur anderen Seite.
Kräfte verlaufen Strahlenförmig, da ist die Idee mit dem Lagerbock von BMW mit den Scheiben, nicht optimal. In der 90 Grad Ecke zwischen Scheibe und Bock wird der Kraftfluss unterbrochen. Dieses galt es zu ändern.
Ein weiterer Grundsatz, je mehr Teile, je ungenauer wird es. Stichwort Summenspiel. Anders herum, je weniger und genauer, desto aufwendiger die Fertigung.
Also wollte ich ein Teil aus möglichst wenigen Bauteilen.
In der Praxis hatte ich festgestellt, dass noch ein Effekt eintritt. Oft ist das Spiel an der Welle, unterschiedlich wenn man unter dieser und oben drüber prüft. Entweder Verspannt es sich beim anziehen, oder durch einarbeiten in die Köpfe (Planen).
Oft wurde hier geschrieben und bebildert, dass die Böcke regelrecht in den Kopf einarbeiten. Auch hier ist die Ursache ein einfaches Problem der Mechanik: Kraft pro Fläche! Die Böcke von Powerboxer, welche auch Granada fertigt, liegen einfach nicht auf der dafür vorgesehenen Fläche, sondern kleiner auf. Die Kraft ist jedoch die Selbe, die Einleitung der Selbigen in den Kopf ist schlecht.
Also ist es wichtig, eine Bauform zu wählen, welche die Kraft ideal einleitet und auf ganzer Fläche aufliegt.
Anfangs wollte ich noch oben drüber einen Bügel haben mittels Passung, ähnlich wie Weierstall es hat. Das Teil ist aber nur als Schmiedeteil zu realisieren, ich habe es versucht wie auf den ersten Bilder mit den Passungen oben zu sehen ist, musste es aber fertigungstechnisch verwerfen.
Ein weiteres Kriterium ist die Mutter, welche bei den Powerboxerteilen und dem ungünstigen Winkel, auch kleine gute Krafteinleitung gewährleistet. Hier stellte sich die BMW Lösung als ideal heraus bezüglich des Winkels.
Viele Leute verbauen die Teile nicht aufgrund ihres Gewichtes. Das war für mich 100% nachvollziehbar!
Mann (Frau auch!), muss aber sehen, die Teile von Powerboxer sind eine Lösung, welche Fertigungstechnisch unter berücksichtigung der geringsten Kosten, entstanden ist. Mit ganz geringem Aufwand und Laufzeiten der Maschine, ein solches Teil zu bauen.
Wer hier so meine Sachen verfolgt, sieht schnell, dass ich immer nach der besten Lösung strebe ohne Rücksicht auf Aufwand.
Es ist das Eine etwas nachzubauen, das andere sich damit auseinander zu setzen, zu analysieren, eine Verbesserung zu erwirken, es zu fertigen. Alle meine Teile baue ich schlussendlich selber, konstruiere diese und schreibe die Programme. Made in Germany, wenn man so will.
Keine Weltneuheit, kein Quantensprung, aber eine Verbesserung im Detail.
Der Ertrag/Aufwand steht hier in keinem Verhältnis.
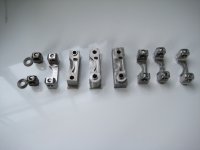
Auf dem Bild mal Einige Teile und Versuchsmuster…….die anderen Teile sind gerade beim Trowalisieren.
Links original BMW Gewicht 158,16 Gramm
2 von li. Powerboxer 255,77 Gramm ohne Zentrierhülse
2von re. Prototyp noch mit 3D Innengeometrie 42CroMo4 +qt
Ganz rechts, fertiger Kipphebelbock von mir noch ohne Schlitze, Material Titan mit einer Festigkeit 20% über dem Pedant aus Stahl und mit einem Gewicht von 113,14 Gramm!
Das Selbe Teil werde ich in 42CrMo zum Verkauf anbieten. Gewicht reiche ich nach.
Hier noch Bilder (zum Nachbauen…….)
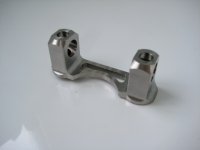
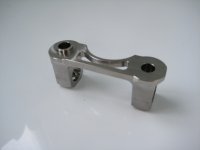
Eine weitere Überlegung geht imo dahin, das ein Ölfilm bis 3/100mm voll tragfähig ist. Was soll das jetzt sagen? Ich werde die Kunststoffscheibe durch Lagerbronze ersetzen und pro Kipphebel/Lagerbock gesondert auf 1-2/100mm anfertigen. Rein in der Theorie, müsste ein Kontakt der beiden Bauteile damit ausgeschlossen werden und das Geräusch gänzlich eliminiert werden.
Ich halte euch auch dem laufenden, versprochen!
Jetzt habe ich da noch eine Nockenwellenaktion am Bein an dessen Ende wohl eine Nocke stehen wird, die Extra für mein Motor berechnet und gefertigt wird. Jetzt bin ich gerade dran mir noch Titanpleuel zu bauen, ihr seht die Projekte hören nicht auf.
In diesem Sinne:
Gruß Marco
Seit Monaten bin ich an den Dingern dran. Was sich hier so einfach präsentiert, war ein ganz steiniger Weg! So viel Pleiten, Pech und Pannen, das glaubt man nicht.
Zielsetzung war ein einteiliger Kipphebelbock der das Klappern im Ventiltrieb minimiert.
Wie geht man an so etwas heran? Für Maschinenbauer eine klare Sache, für den Laien möchte ich es erläutern.
Als erstes muss man sich klar machen, welche Kräfte wo herrschen und wie deren Verlauf ist. Da haben wir zu einen die Vorspannung der Stehbolzen zum Motor, zum anderen die Wärmedehnung in der 90 Grad Achse zur anderen Seite.
Kräfte verlaufen Strahlenförmig, da ist die Idee mit dem Lagerbock von BMW mit den Scheiben, nicht optimal. In der 90 Grad Ecke zwischen Scheibe und Bock wird der Kraftfluss unterbrochen. Dieses galt es zu ändern.
Ein weiterer Grundsatz, je mehr Teile, je ungenauer wird es. Stichwort Summenspiel. Anders herum, je weniger und genauer, desto aufwendiger die Fertigung.
Also wollte ich ein Teil aus möglichst wenigen Bauteilen.
In der Praxis hatte ich festgestellt, dass noch ein Effekt eintritt. Oft ist das Spiel an der Welle, unterschiedlich wenn man unter dieser und oben drüber prüft. Entweder Verspannt es sich beim anziehen, oder durch einarbeiten in die Köpfe (Planen).
Oft wurde hier geschrieben und bebildert, dass die Böcke regelrecht in den Kopf einarbeiten. Auch hier ist die Ursache ein einfaches Problem der Mechanik: Kraft pro Fläche! Die Böcke von Powerboxer, welche auch Granada fertigt, liegen einfach nicht auf der dafür vorgesehenen Fläche, sondern kleiner auf. Die Kraft ist jedoch die Selbe, die Einleitung der Selbigen in den Kopf ist schlecht.
Also ist es wichtig, eine Bauform zu wählen, welche die Kraft ideal einleitet und auf ganzer Fläche aufliegt.
Anfangs wollte ich noch oben drüber einen Bügel haben mittels Passung, ähnlich wie Weierstall es hat. Das Teil ist aber nur als Schmiedeteil zu realisieren, ich habe es versucht wie auf den ersten Bilder mit den Passungen oben zu sehen ist, musste es aber fertigungstechnisch verwerfen.
Ein weiteres Kriterium ist die Mutter, welche bei den Powerboxerteilen und dem ungünstigen Winkel, auch kleine gute Krafteinleitung gewährleistet. Hier stellte sich die BMW Lösung als ideal heraus bezüglich des Winkels.
Viele Leute verbauen die Teile nicht aufgrund ihres Gewichtes. Das war für mich 100% nachvollziehbar!
Mann (Frau auch!), muss aber sehen, die Teile von Powerboxer sind eine Lösung, welche Fertigungstechnisch unter berücksichtigung der geringsten Kosten, entstanden ist. Mit ganz geringem Aufwand und Laufzeiten der Maschine, ein solches Teil zu bauen.
Wer hier so meine Sachen verfolgt, sieht schnell, dass ich immer nach der besten Lösung strebe ohne Rücksicht auf Aufwand.
Es ist das Eine etwas nachzubauen, das andere sich damit auseinander zu setzen, zu analysieren, eine Verbesserung zu erwirken, es zu fertigen. Alle meine Teile baue ich schlussendlich selber, konstruiere diese und schreibe die Programme. Made in Germany, wenn man so will.
Keine Weltneuheit, kein Quantensprung, aber eine Verbesserung im Detail.
Der Ertrag/Aufwand steht hier in keinem Verhältnis.
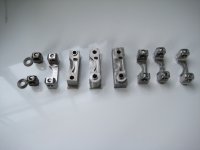
Auf dem Bild mal Einige Teile und Versuchsmuster…….die anderen Teile sind gerade beim Trowalisieren.
Links original BMW Gewicht 158,16 Gramm
2 von li. Powerboxer 255,77 Gramm ohne Zentrierhülse
2von re. Prototyp noch mit 3D Innengeometrie 42CroMo4 +qt
Ganz rechts, fertiger Kipphebelbock von mir noch ohne Schlitze, Material Titan mit einer Festigkeit 20% über dem Pedant aus Stahl und mit einem Gewicht von 113,14 Gramm!
Das Selbe Teil werde ich in 42CrMo zum Verkauf anbieten. Gewicht reiche ich nach.
Hier noch Bilder (zum Nachbauen…….)
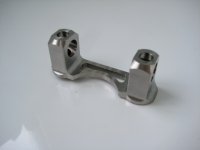
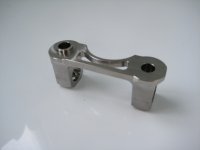
Eine weitere Überlegung geht imo dahin, das ein Ölfilm bis 3/100mm voll tragfähig ist. Was soll das jetzt sagen? Ich werde die Kunststoffscheibe durch Lagerbronze ersetzen und pro Kipphebel/Lagerbock gesondert auf 1-2/100mm anfertigen. Rein in der Theorie, müsste ein Kontakt der beiden Bauteile damit ausgeschlossen werden und das Geräusch gänzlich eliminiert werden.
Ich halte euch auch dem laufenden, versprochen!
Jetzt habe ich da noch eine Nockenwellenaktion am Bein an dessen Ende wohl eine Nocke stehen wird, die Extra für mein Motor berechnet und gefertigt wird. Jetzt bin ich gerade dran mir noch Titanpleuel zu bauen, ihr seht die Projekte hören nicht auf.
In diesem Sinne:
Gruß Marco