Hi @all
Als ich mir die Titan-Federteller bei Israel bestellte, gingen natürlich auch die dort angebotenen
" leichten Einstellschrauben " nicht an mir vorbei.
Doch da kam der Bastlergeist und sprach: versuch ma was !
OK, gibt´s sicher schon aber ich freu mich trotzdem darüber :]
Eingangsmessung
Schraube ohne Mutter = 10,8 gr
Mutter = 2,7 gr
gesamt = 13,5 gr
So, jetzt hab ich angefangen, die Schrauben hohl zu bohren. Dazu erstmal das Ende des Gew. plan gedreht
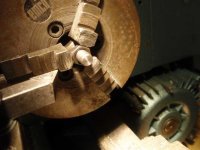
dann mit Zentrierbohrer angebohrt
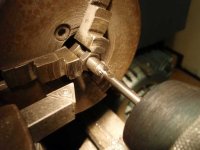
in 2 Schritten auf 4 mm gebracht, es hart des Zeugs
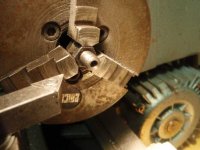
und dann noch den Sechkant der Pfanne etwas abgenommen
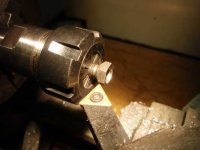
Und so sieht die Schraube dann aus
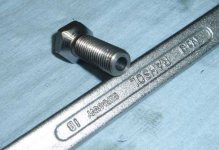
Fertigmessung
Schraube jetzt 8,2 gr
+ Mutter 2,8 gr
Gesamt 11,0 gr
OK, das sind jetzt nur 2,5 Gramm pro Schraube, aber die Titanteller sind auch nur 3 Gramm leichter als die originalen 16 Gramm-Teller.
Also ähnlicher Efekkt an gleicher Stelle.
Ich bin zufrieden. Vielleicht geht noch etwas mehr, aber es soll ja auch halten
Als ich mir die Titan-Federteller bei Israel bestellte, gingen natürlich auch die dort angebotenen
" leichten Einstellschrauben " nicht an mir vorbei.
Doch da kam der Bastlergeist und sprach: versuch ma was !
OK, gibt´s sicher schon aber ich freu mich trotzdem darüber :]
Eingangsmessung
Schraube ohne Mutter = 10,8 gr
Mutter = 2,7 gr
gesamt = 13,5 gr
So, jetzt hab ich angefangen, die Schrauben hohl zu bohren. Dazu erstmal das Ende des Gew. plan gedreht
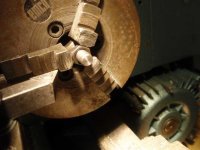
dann mit Zentrierbohrer angebohrt
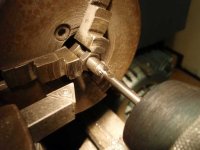
in 2 Schritten auf 4 mm gebracht, es hart des Zeugs
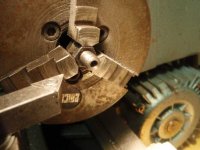
und dann noch den Sechkant der Pfanne etwas abgenommen
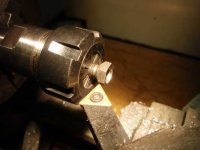
Und so sieht die Schraube dann aus
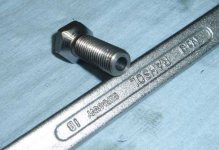
Fertigmessung
Schraube jetzt 8,2 gr
+ Mutter 2,8 gr
Gesamt 11,0 gr
OK, das sind jetzt nur 2,5 Gramm pro Schraube, aber die Titanteller sind auch nur 3 Gramm leichter als die originalen 16 Gramm-Teller.
Also ähnlicher Efekkt an gleicher Stelle.
Ich bin zufrieden. Vielleicht geht noch etwas mehr, aber es soll ja auch halten

Anhänge
Zuletzt bearbeitet: